R2W-3
Automatic Pipe Welding Equipment
Introducing R2W-3, our automatic pipe welding machine that gives you the flexibility to use TIG and MIG on the same platform.
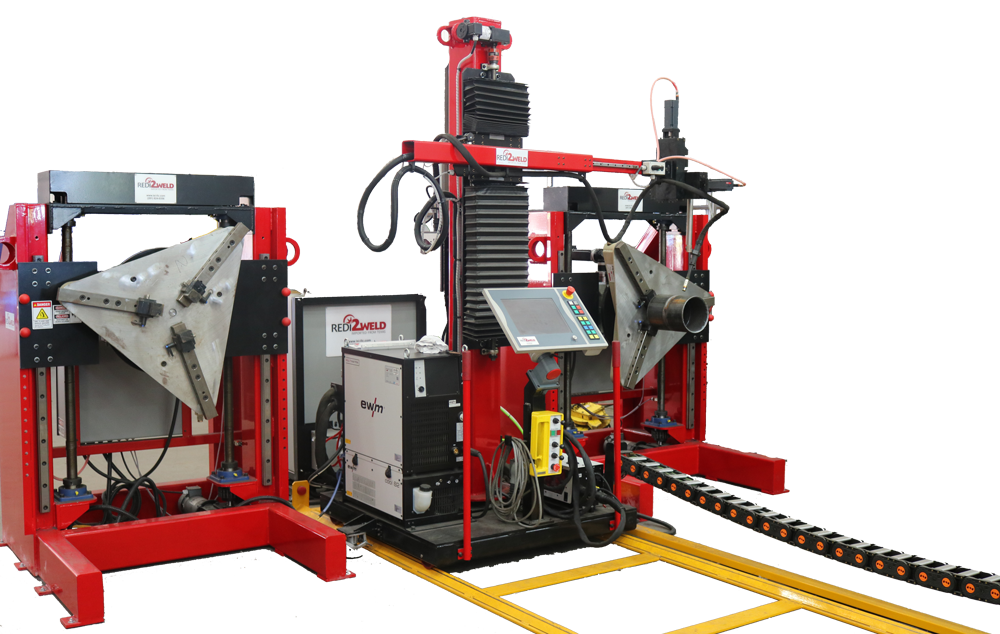
For the Modern Fabricator
In addition to the flexibility to use TIG and MIG on the same automated pipe welding platform, R2W-3 can be configured with parallel headstocks and a column and boom that can articulate 180 degrees. This makes it so your operator can simply rotate the column and boom 180 degrees, keeping the arc time at a high level of efficiency.
Our systems are designed to evolve with you. You can easily expand the number of headstocks, extend the system, or add MIG and TIG capabilities as your needs grow. It’s a machine that’s built to adapt, just like your business.
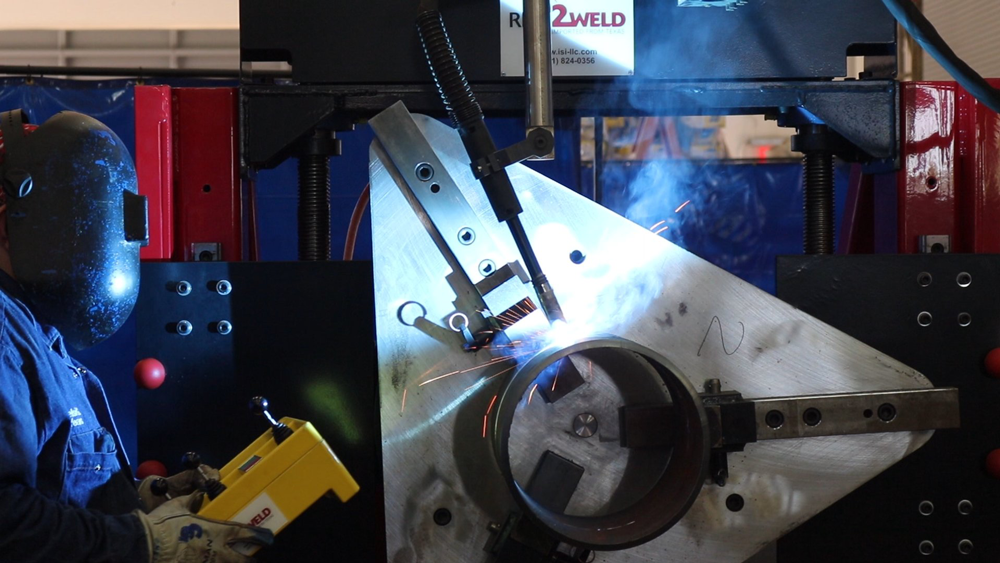
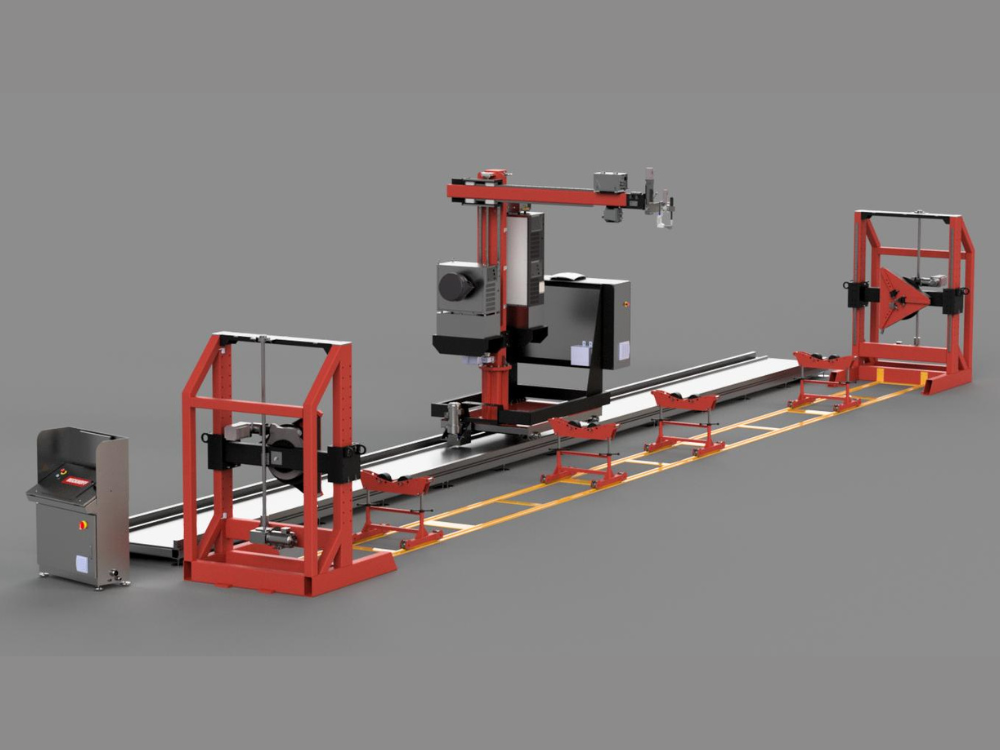
Additional Options
Additional wire feeders for both MIG and TIG systems
Drum wire feed (250 & 500 lb capacity)
Manual torch on board to allow for repairs to welds or manual welding of joints that cannot be fit “correctly”
EWM XNet weld Data Recording
Additional pipe supports
Vessel welding with “growing line” using integrated turning rolls
Linear or long seam welding functionality
Main Components
Redi2Weld is designed with productivity in mind. The mobile welding cart is driven on either hardened machine rails with linear bearings (in the case of the pipe/vessel welding systems) using a helical gear rack and encoder-equipped drive motors or via a robust rack and pinion system with high-precision guide rollers for the pipe welding system.
The cart also holds the Column and Boom with optional rotation capacity, power supplies (MIG – TIG or BOTH), control cabinet and optional drum feed. The boom features the ability to tilt the torch to allow for welding of socket welds and slip-on flanges. All of this comes with efficient and discrete cable management and single-source power to afford a safer and cleaner work environment.
The Redi2Weld headstocks and rotation solutions are designed in house and are manufactured by Redi2Weld. We use extremely high precision slew ring bearings to both accurately rotate pipe spools at a precise speed and to prevent any backlash or vibration in the rotation when encountering moments of inertia.
Headstocks come with mechanized vertical travel to afford the adjustment of centerline of the pipe spool and to afford the swing of longer tangent branch connections. Headstocks come with a 3 jaw gripper with hardened teeth to ensure a safe and secure operation. Gripper sizes are set according to your needs.
Redi2Weld R2W-3 systems utilize EWM Automation Series Power supplies. In each R2W-3 system you have the option of configuring the system for MIG/FCAW only OR TIG/Hot Wire TIG only. Alternately, you can choose to configure your system with both MIG and TIG functionality.
Redi2Weld also gives you the flexibility to add either MIG or TIG functionality at a later date to afford you greater control over your budget and implementation cost.
Standard MIG
Standard MIG systems include the EWM Phoenix 552 power supply and water cooler for MIG/MAG modes including: MIG, FCAW and Metal Core. The Phoenix 552 provides up to 550 amps of current while allow you to weld with RootArc (modified short circuit for rooting), ForceArc (highly advanced spray mode) or ForceArc Puls (highly advanced spray mode with pulse technology).
Standard TIG
Standard TIG systems include the EWM Tetrix 352 power supply with Hot Wire capability and the TIGSPEED Robo Feed wire feed system that provides wire oscillation as well as hot wire current. The Tetrix 352 provides 350 amps of current, 180 amps of hot wire current, and wire oscillation of up to 16Hz.
Standard TIG systems include the EWM Tetrix 352 power supply with Hot Wire capability and the TIGSPEED Robo Feed wire feed system that provides wire oscillation as well as hot wire current. The Tetrix 352 provides 350 amps of current, 180 amps of hot wire current, and wire oscillation of up to 16Hz.
The weld camera allows the operator to be removed from the welding arc to operate and remotely monitor the process through an HMI PC without the need of a welding helmet. This helps to reduce the risk of any operator fatigue throughout the multiple welding passes. Altogether the automated system and the Xiris Weld Camera help create welds at a high rate of efficiency and quality.
Designed with operator safety in mind, the remote pendant allows the operator to get away from the arc, and can complete the weld without a hood by using the remote along with the optional Xiris vision system.
Watch Our Virtual Demo
Interested in seeing how our automated welding technology works? Check out our demo video that walks you through everything you need to know about Redi2Weld.
If you’re interested in learning more or want an in-person demo, reach out to our leadership team today.
Download the R2W-3 Technical Brochure
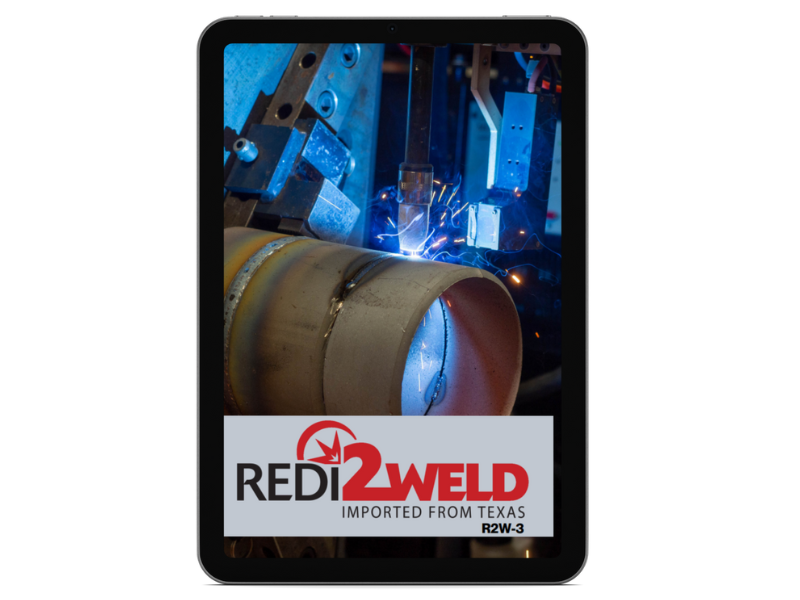